GKN Aerospace joined tier one industry partners Airbus, AgustaWestland, GE, Rolls-Royce, Cytec and Vestas last week to celebrate the official opening of the second phase of the UK’s
highly successful National Composites Centre (NCC).
Established just three years ago, the NCC is already at the heart of the UK’s fast-growing expertise in the design and rapid manufacture of composites - a key focus of the UK
government’s long term industrial strategy.
The new building will greatly increase the NCC’s total floor area, extending valuable accommodation for teams from collaborating organisations and academia. It also increases the scope
and diversity of the state-of-the-art equipment based on site which is helping prove faster, more effective production techniques for composite structures.
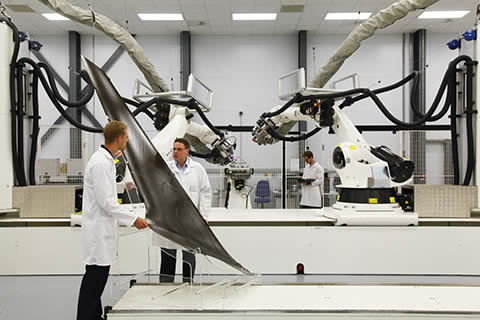 |
Innovative winglet lower skin manufacture, using robotic fibre placement at the
NCC : Photo courtesy of the NCC |
Ian Chatting, Vice President, Technology, GKN Aerospace comments: "The NCC is proving a highly effective ‘catapult centre’ for the UK aerospace sector. This new facility will extend the
support it can offer us, speeding our progress towards proving new technologies and processes that will ensure the UK remains successful in the growing, but ever-more competitive,
global aerospace market.”
Since the opening of the NCC, GKN Aerospace has used the centre’s facilities to support both short and long term development activities. GKN Aerospace has a team of thirty
technologists and engineers based at the NCC working with industrial partners and NCC colleagues on a number of strategically important projects and there have already been
successes. The company has used the NCC’s automated fibre placement technology in the manufacture of an innovative winglet design that is lighter, has fewer parts and will be 20%
cheaper to manufacture than current production winglets. Vital structural analysis techniques that were evolved within
NCC-based projects are in use in producing large, flight-critical wing
structures at one of the company’s UK sites. Simultaneously, longer term collaborative projects are now based at the NCC and are exploring ‘natural laminar flow’ flight which will lead to
new, ultra-efficient wing designs for future aircraft.
Chatting continues: “The NCC speeds the progress of our in-house R&D activity in two ways: by providing a facility that is shared on an equal basis with industrial and academic partners
which allows a far greater level of openness and collaboration within and across UK manufacturing sectors; and by offering partners the opportunity to thoroughly explore the potential of
innovative, state-of-the-art, high capital-cost manufacturing equipment.”
GKN Aerospace has been a major force in extending the use of high performance composites in aviation worldwide. The company is the leading first tier supplier of composites and is at
the forefront of the drive to introduce of automated, robotic manufacturing techniques that are making composites manufacture faster and far more consistent. GKN Aerospace is now
exploring innovations in future composite wing and engine structure design that will improve aircraft performance and cut manufacturing costs through increased automation, reduced
materials wastage and simplified assembly.
|